Ví dụ thực tế ứng dụng phương pháp 5S trong doanh nghiệp
5S là một phương pháp quản lý và tổ chức môi trường làm việc hiệu quả, được phát triển và hoàn thiện tại Nhật Bản. Phương pháp 5S không chỉ đơn thuần là một công cụ sắp xếp văn phòng, mà còn là một triết lý quản lý toàn diện, tạo nền tảng vững chắc cho việc xây dựng văn hóa doanh nghiệp chuyên nghiệp và hiệu quả.
Khi áp dụng đúng cách, 5S mang lại nhiều lợi ích thiết thực cho doanh nghiệp: nâng cao năng suất lao động, giảm thiểu lãng phí, cải thiện chất lượng sản phẩm, đảm bảo an toàn nơi làm việc và tăng cường tinh thần làm việc của nhân viên. Hãy cùng Asiasoft tìm hiểu chi tiết về các ví dụ ứng dụng phương pháp 5S trong doanh nghiệp.
1. Tổng quan về phương pháp 5S
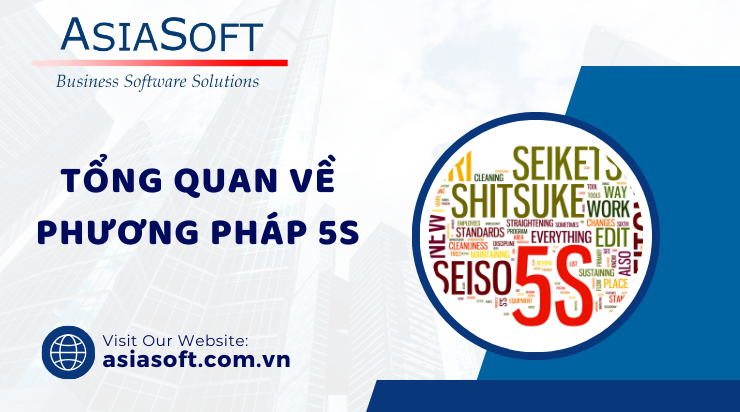
1.1. 5S là gì?
5S là một phương pháp quản lý và tổ chức không gian làm việc có nguồn gốc từ Nhật Bản. Phương pháp này bao gồm 5 nguyên tắc cốt lõi, mỗi nguyên tắc đều bắt đầu bằng chữ S trong tiếng Nhật:
- Seiri (整理 – Sàng lọc): Phân loại và loại bỏ những vật dụng không cần thiết, chỉ giữ lại những gì thực sự cần dùng. Điều này giúp tối ưu hóa không gian và nguồn lực.
- Seiton (整頓 – Sắp xếp): Bố trí mọi thứ một cách khoa học, theo nguyên tắc “một chỗ cho mọi thứ, mọi thứ đúng chỗ của nó”. Việc này đảm bảo dễ tìm, dễ lấy, dễ sử dụng và dễ trả về đúng vị trí.
- Seiso (清掃 – Sạch sẽ): Duy trì môi trường làm việc luôn sạch sẽ, ngăn nắp. Không chỉ là vệ sinh đơn thuần mà còn bao gồm việc bảo dưỡng thiết bị và không gian làm việc.
- Seiketsu (清潔 – Săn sóc): Thiết lập và duy trì các tiêu chuẩn để đảm bảo ba bước trên được thực hiện đều đặn. Bao gồm việc xây dựng quy trình, hướng dẫn và kiểm tra định kỳ.
- Shitsuke (躾 – Sẵn sàng): Rèn luyện tính kỷ luật, tự giác trong việc duy trì và cải tiến liên tục 4S đầu tiên. Đây là bước quan trọng nhất, đòi hỏi sự cam kết từ mọi thành viên trong tổ chức.
Trong tiếng Anh, 5S được dịch thành: Sort (Sàng lọc), Set in Order (Sắp xếp), Shine (Sạch sẽ), Standardize (Săn sóc), và Sustain (Sẵn sàng). Đây không đơn thuần là một bộ công cụ quản lý, mà là một triết lý toàn diện giúp xây dựng văn hóa làm việc hiệu quả và chuyên nghiệp.
1.2. Nguồn gốc của 5S
5S là một trong những trụ cột quan trọng của “Hệ thống sản xuất Toyota” (TPS), được phát triển và hoàn thiện tại Nhật Bản vào những năm 1950. Phương pháp này ra đời từ nhu cầu thực tế về việc tối ưu hóa quy trình sản xuất và nâng cao hiệu quả làm việc trong môi trường công nghiệp sau Thế chiến II.
Hệ thống này sau đó được phát triển thành phương pháp sản xuất tinh gọn (Lean Manufacturing), một triết lý quản lý toàn diện nhằm tối đa hóa giá trị cho khách hàng thông qua việc loại bỏ lãng phí và tối ưu hóa quy trình.
Trong hệ sinh thái của sản xuất tinh gọn, 5S đóng vai trò nền tảng, kết hợp chặt chẽ với các công cụ quản lý tiên tiến khác như Kaizen (cải tiến liên tục), Kanban (hệ thống quản lý công việc trực quan), Jidoka (tự động hóa thông minh), và Poka-yoke (ngăn ngừa lỗi).
Tầm quan trọng của 5S trong môi trường sản xuất hiện đại thể hiện ở nhiều khía cạnh:
- Nền tảng cải tiến: 5S tạo môi trường làm việc có tổ chức, là điều kiện tiên quyết cho việc áp dụng các công cụ cải tiến khác.
- Hiệu quả vận hành: Một nơi làm việc được tổ chức tốt giúp giảm thiểu thời gian tìm kiếm, di chuyển và xử lý công việc.
- An toàn lao động: Môi trường làm việc ngăn nắp, sạch sẽ giúp giảm thiểu rủi ro tai nạn và sự cố trong sản xuất.
- Chất lượng sản phẩm: Quy trình làm việc chuẩn hóa và môi trường có tổ chức giúp giảm thiểu lỗi và nâng cao chất lượng đầu ra.
2. Vai trò của phương pháp 5S với doanh nghiệp
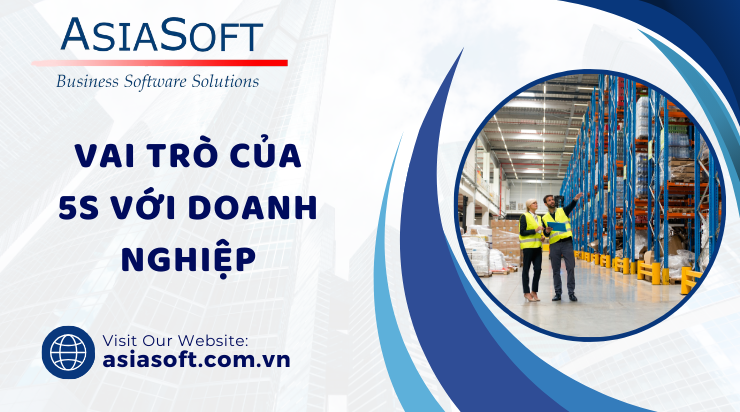
Phương pháp 5S có vai trò rất quan trọng với doanh nghiệp. Nó giúp tạo ra một môi trường làm việc hiệu quả, cải thiện sự tổ chức và năng suất, giảm thiểu lãng phí trong quá trình sản xuất và kinh doanh. Các lợi ích cụ thể của 5S đối với doanh nghiệp bao gồm:
- Tăng năng suất. 5S giúp tối ưu hóa không gian làm việc (cả hiện trường và không gian số) và quy trình làm việc, tiết kiệm thời gian và nỗ lực; đồng thời, cải thiện chất lượng sản phẩm và dịch vụ, tạo ra giá trị cao hơn cho khách hàng.
- Giảm chi phí. 5S giúp giảm thiểu lãng phí, bao gồm cả lãng phí thời gian, nguyên vật liệu và nhân lực. Điều này giúp tăng lợi nhuận và cạnh tranh cho doanh nghiệp.
- Cải thiện sự tổ chức. 5S giúp tạo ra một môi trường làm việc có tổ chức tốt. Từ đó, giúp các nhân viên tìm kiếm và truy cập thông tin, tài liệu dễ dàng hơn.
- Tăng sự an toàn. 5S giúp tạo ra một môi trường làm việc an toàn hơn; giảm nguy cơ tai nạn lao động và bảo vệ sức khỏe của nhân viên.
- Nâng cao chất lượng. 5S giúp giảm thiểu sai sót trong quá trình sản xuất và kinh doanh; tăng độ tin cậy và chất lượng sản phẩm dịch vụ; giúp doanh nghiệp đáp ứng được nhu cầu của khách hàng và tăng cường sự tin tưởng của họ.
3. Ví dụ về phương pháp 5S trong thực tế
3.1. Công ty Samsung Electronics Việt Nam – Áp dụng phương pháp 5S trong công nghiệp điện tử
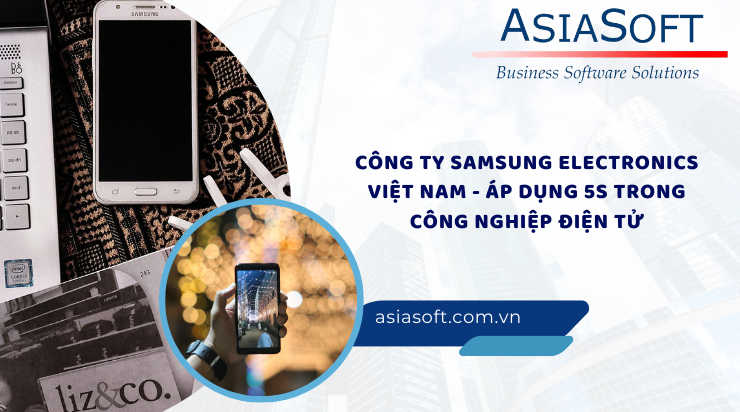
Samsung Electronics Việt Nam (SEV) đã triển khai mô hình 5S một cách toàn diện tại các nhà máy sản xuất điện tử của mình. Việc áp dụng 5S được thực hiện song song với các tiêu chuẩn sản xuất quốc tế khác.
Kết quả đạt được sau khi áp dụng 5S:
- Giảm 40% thời gian tìm kiếm linh kiện và thiết bị
- Tăng năng suất lao động 25%
- Giảm tỷ lệ sản phẩm lỗi từ 2.5% xuống 0.8%
- Tiết kiệm 15% chi phí vận hành
Samsung đã xây dựng quy trình đánh giá 5S nghiêm ngặt:
- Kiểm tra hàng ngày tại các trạm sản xuất
- Đánh giá chéo giữa các bộ phận hàng tuần
- Audit toàn diện hàng tháng với sự tham gia của ban lãnh đạo
Điểm nổi bật trong cách triển khai 5S của Samsung là việc tích hợp với hệ thống quản lý chất lượng thông minh, sử dụng công nghệ IoT để giám sát và đánh giá hiệu quả thực hiện 5S theo thời gian thực.
3.2. Vinamilk – Ứng dụng phương pháp 5S trong ngành sữa
Vinamilk là một ví dụ điển hình về việc áp dụng thành công mô hình 5S trong ngành công nghiệp thực phẩm. Doanh nghiệp này đã triển khai 5S tại tất cả các nhà máy và trang trại của mình.
Những thành tựu đáng chú ý:
- Cải thiện 50% về vệ sinh an toàn thực phẩm
- Tăng 30% hiệu suất sản xuất
- Giảm 35% chi phí bảo trì thiết bị
- Đạt chứng nhận ISO 9001:2015 và HACCP
Vinamilk đã phát triển một hệ thống đánh giá 5S riêng biệt, phù hợp với đặc thù ngành sữa:
- Đánh giá vệ sinh hàng giờ tại các điểm sản xuất trọng yếu
- Kiểm tra chất lượng và an toàn thực phẩm hàng ngày
- Audit toàn diện về 5S mỗi quý
Thành công của Vinamilk trong việc áp dụng 5S đã góp phần quan trọng giúp doanh nghiệp duy trì vị thế dẫn đầu trong ngành công nghiệp sữa Việt Nam và vươn ra thị trường quốc tế.
3.3. Tập đoàn Toyota – Tiên phong trong áp dụng phương pháp 5S
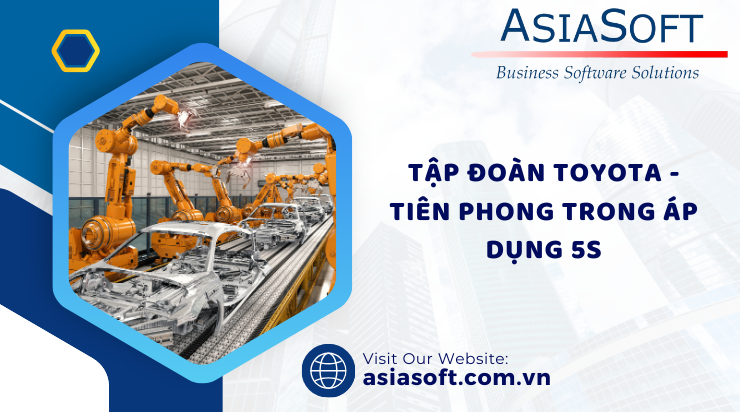
Toyota, tập đoàn sản xuất ô tô hàng đầu thế giới, là một trong những doanh nghiệp tiên phong trong việc áp dụng và phát triển mô hình 5S. Tại các nhà máy Toyota, 5S được xem như nền tảng cơ bản của hệ thống sản xuất tinh gọn (Toyota Production System – TPS).
Một số thành tựu nổi bật của Toyota khi áp dụng 5S:
- Giảm 60% thời gian tìm kiếm công cụ và thiết bị
- Tăng 35% hiệu suất sản xuất tổng thể
- Giảm 45% số lượng tai nạn lao động
- Tiết kiệm 25% chi phí vận hành và bảo trì
Toyota đã xây dựng một hệ thống đánh giá 5S chặt chẽ với các tiêu chí cụ thể:
- Đánh giá hàng ngày: Thực hiện bởi tổ trưởng sản xuất
- Đánh giá hàng tuần: Do quản đốc phân xưởng thực hiện
- Đánh giá hàng tháng: Có sự tham gia của ban giám đốc
Điểm đặc biệt trong cách triển khai 5S của Toyota là việc tích hợp chặt chẽ với các hoạt động kaizen (cải tiến liên tục). Mỗi nhân viên được khuyến khích đóng góp ít nhất 2 đề xuất cải tiến mỗi tháng, tạo nên văn hóa cải tiến mạnh mẽ trong toàn tổ chức.
3.4. Công ty CNCPS – Hành trình chuyển đổi với phương pháp 5S
Trong xu hướng đổi mới và nâng cao hiệu quả sản xuất, Công ty Cổ phần CNCPS tại Bình Dương đã mạnh dạn áp dụng mô hình 5S kết hợp với công cụ quản lý hiệu suất tổng thể (TPM). Đây là bước đi chiến lược nhằm hiện thực hóa tầm nhìn trở thành doanh nghiệp hàng đầu trong ngành sản xuất và gia công sản phẩm nhựa tại Việt Nam.
Quy trình triển khai được thực hiện bài bản, với trọng tâm là tối ưu hóa quy trình sản xuất và cải thiện môi trường làm việc. Điểm đặc biệt trong cách tiếp cận của CNCPS là việc tích hợp 5S với hệ thống TPM, tạo nên một giải pháp toàn diện cho việc quản lý và vận hành nhà máy.
Kết quả đạt được sau 4 tháng triển khai đã vượt xa kỳ vọng ban đầu. Chỉ số hiệu suất thiết bị tổng thể (OEE) đã có bước nhảy vọt từ 51% lên 78%. Đáng chú ý, thời gian dừng máy do sự cố giảm đáng kể từ 5.400 phút xuống còn 1.296 phút, số lần sự cố trong tháng giảm từ 27 xuống 18 lần. Quy trình thay khuôn được tối ưu, giảm từ 75 phút xuống 45 phút. Đặc biệt, tỷ lệ sản phẩm đạt chất lượng tăng từ 90% lên 97%, đồng thời tiết kiệm được 3 triệu đồng chi phí bảo trì cho mỗi máy mỗi năm.
3.5. Áp dụng phương pháp 5S tại Honda – Một câu chuyện thành công
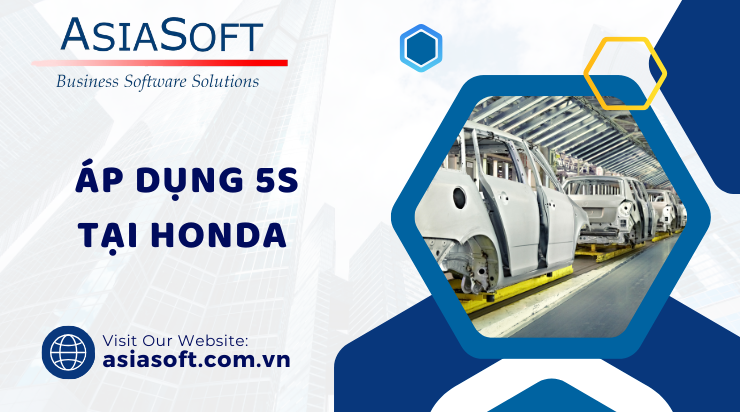
Honda là một ví dụ điển hình về việc áp dụng thành công mô hình 5S trong toàn bộ hệ thống, từ nhà máy sản xuất đến các showroom. Điều đặc biệt trong cách triển khai của Honda là sự nhất quán và cam kết mạnh mẽ từ cấp lãnh đạo đến nhân viên.
Thành công của Honda với 5S thể hiện qua những con số ấn tượng:
- Tăng 25% hiệu suất sản xuất
- Giảm 40% thời gian tìm kiếm công cụ và vật tư
- Cải thiện 30% môi trường làm việc
Honda đã xây dựng một hệ thống quản lý 5S độc đáo với ba cấp độ đánh giá:
- Sàng lọc thông minh: Áp dụng hệ thống phân loại ba màu:
- Nhãn đỏ: Đánh dấu vật dụng cần loại bỏ
- Nhãn xanh: Xác định vật dụng cần thiết thường xuyên
- Nhãn vàng: Đánh dấu vật dụng có thể cần trong tương lai
- Sắp xếp hiệu quả: Honda áp dụng “Quy tắc 30 giây” – một tiêu chuẩn độc đáo đảm bảo mọi vật dụng có thể được tìm thấy trong vòng 30 giây. Quy tắc này không chỉ tiết kiệm thời gian mà còn tạo ra một môi trường làm việc có tổ chức.
- Duy trì và cải tiến liên tục: Công ty thực hiện đánh giá 5S hàng tuần, với sự tham gia của các cấp quản lý. Điều này đảm bảo tiêu chuẩn được duy trì và không ngừng cải thiện.
Kết quả nổi bật nhất của việc áp dụng 5S tại Honda là sự thay đổi trong văn hóa doanh nghiệp. Nhân viên không chỉ tuân thủ các quy tắc 5S mà còn chủ động đề xuất cải tiến, tạo nên một môi trường làm việc năng động và sáng tạo. Điều này đã góp phần quan trọng vào việc duy trì vị thế của Honda như một trong những nhà sản xuất ô tô và xe máy hàng đầu thế giới.
3.6. Hành trình chuyển đổi ấn tượng của Công ty TNHH Hóa dệt Hà Tây
Nhận thức được tầm quan trọng của đổi mới trong quản lý sản xuất, Công ty TNHH Hóa dệt Hà Tây đã mạnh dạn triển khai mô hình 5S trên quy mô toàn doanh nghiệp. Dự án được khởi động với sự tư vấn chuyên môn từ các chuyên gia hàng đầu, bắt đầu từ việc đánh giá kỹ lưỡng tiềm năng và khả năng thực thi.
Điểm đặc biệt trong cách tiếp cận của công ty là việc áp dụng đồng bộ 5S tại tất cả các bộ phận: từ kho nguyên liệu, các xưởng sản xuất (may, mẫu, gò, cán luyện) đến khu vực văn phòng. Chiến lược này đảm bảo tính nhất quán và hiệu quả trong quá trình chuyển đổi.
Ông Nguyễn Thanh Tùng, Giám đốc công ty, nhấn mạnh: “5S không đơn thuần là một công cụ quản lý, mà đã trở thành DNA trong văn hóa sản xuất của chúng tôi. Ban lãnh đạo cam kết đầu tư mọi nguồn lực cần thiết để đảm bảo sự thành công của dự án này.”
Sau 12 tháng triển khai, những kết quả đạt được đã vượt xa kỳ vọng ban đầu:
- Môi trường làm việc được cải thiện rõ rệt với hệ thống biển báo khoa học, giúp tối ưu thời gian tìm kiếm và vận hành
- Văn hóa doanh nghiệp chuyển biến tích cực, với 100% nhân viên chủ động thực hiện 5S như một thói quen hàng ngày
- Hiệu quả sử dụng không gian tăng 10%, tạo thêm diện tích cho hoạt động sản xuất
- Năng suất sản xuất tăng ấn tượng: 11,3% trong tháng đầu tiên (từ 83.840 lên 95.111 đôi giày) và duy trì mức tăng 11,6% sau một năm
Thành công của Công ty TNHH Hóa dệt Hà Tây là một minh chứng sinh động cho việc áp dụng hiệu quả mô hình 5S trong doanh nghiệp Việt Nam, đồng thời khẳng định rằng với cam kết mạnh mẽ và phương pháp triển khai bài bản, mọi doanh nghiệp đều có thể đạt được những kết quả tương tự.
4. Phương pháp 5S trong đời sống hàng ngày
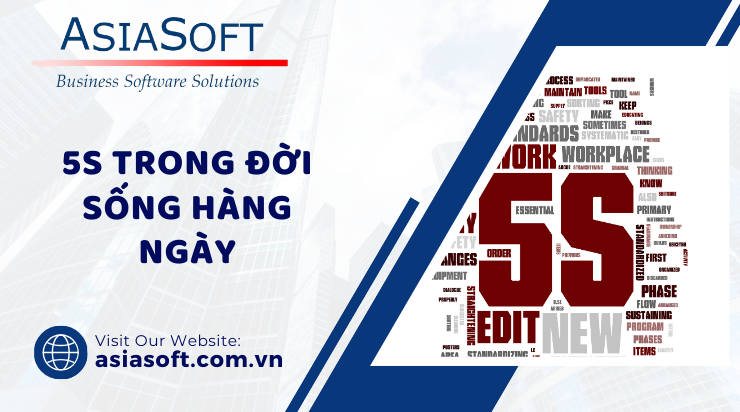
5S không chỉ giới hạn trong môi trường doanh nghiệp mà còn có thể áp dụng hiệu quả trong cuộc sống cá nhân. Việc áp dụng 5S giúp tối ưu hóa không gian sống, nâng cao chất lượng cuộc sống và tạo thói quen tốt.
Một số lợi ích khi áp dụng 5S trong cuộc sống:
- Không gian sống gọn gàng, ngăn nắp và dễ dàng tìm kiếm đồ đạc
- Tiết kiệm thời gian và công sức trong việc dọn dẹp, sắp xếp
- Giảm stress và tăng năng suất trong công việc cá nhân
- Tạo môi trường sống lành mạnh và thoải mái hơn
Để duy trì hiệu quả của 5S, cần thực hiện đều đặn và xem đây như một phần không thể thiếu trong thói quen sinh hoạt hàng ngày. Việc áp dụng 5S không chỉ mang lại lợi ích về mặt vật chất mà còn góp phần hình thành lối sống có kỷ luật và khoa học hơn.